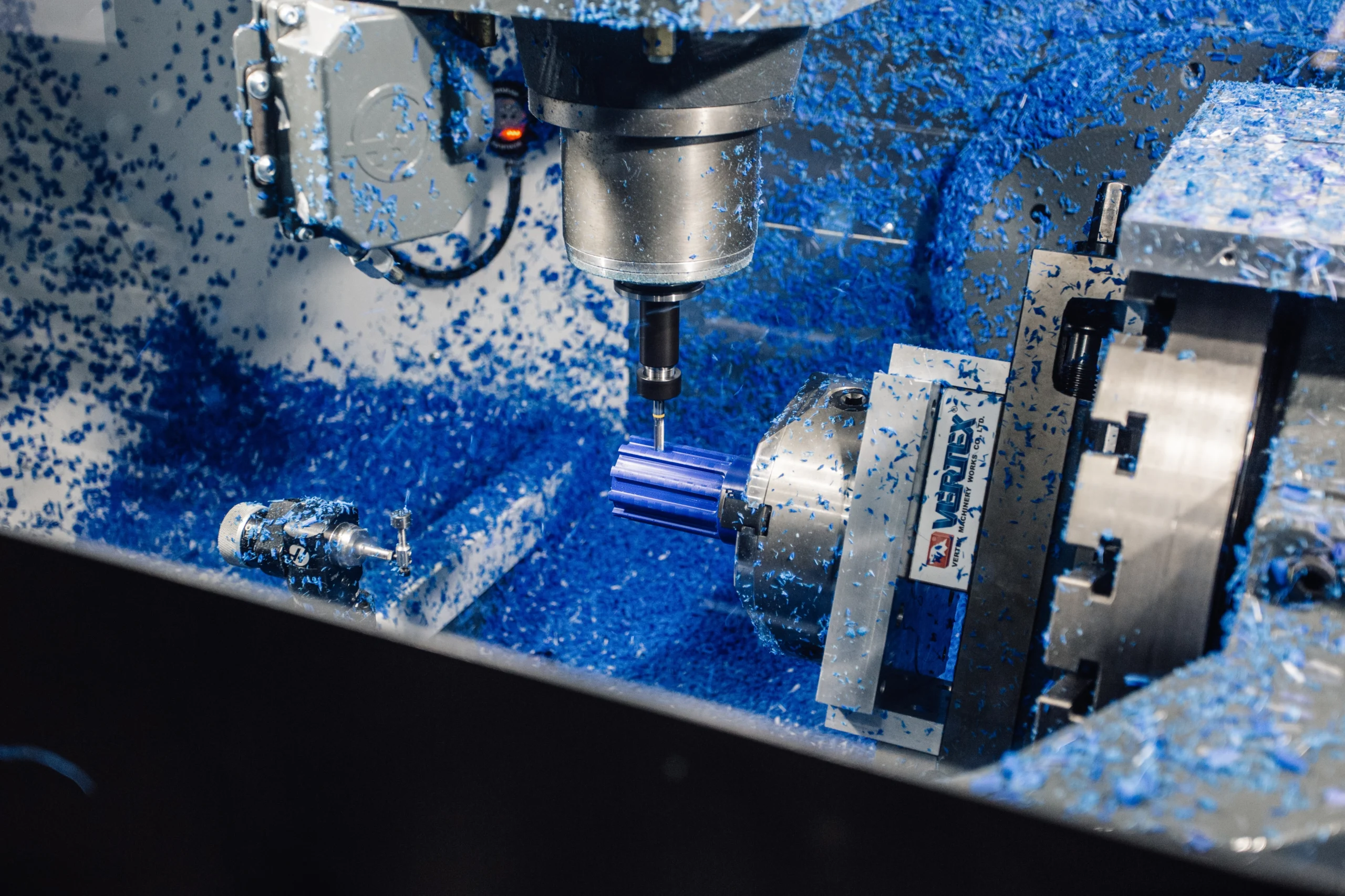
Machining of
plastics
Machining of plastics
Machining of plastics refers to the processing of plastic materials using machining techniques such as turning, milling, drilling, and grinding. These methods are employed to shape, finish, or refine plastic components. Machining plastics requires specific techniques and considerations due to the distinct properties of plastics compared to metals or wood. Here is an overview of the key aspects of plastic machining.
Properties of Plastics Influencing Machining
Hard vs. Soft Plastics: Plastics range from hard and brittle (like polycarbonate) to soft and flexible (like polyethylene). Harder plastics can be more challenging to machine and may cause faster tool wear, while softer plastics are easier to machine but more prone to deformation.
Melting Point: Plastics have varying melting points, which affect the choice of cutting speed and cooling agents. High cutting speeds can cause overheating, leading to melting or deformation of the material.
Thermal Expansion: Plastics can expand or contract with temperature changes, which must be considered during machining and fitting parts.
Machining Techniques
Turning:
In turning, cutting tools are applied to a rotating workpiece. Proper control of cutting speeds and feed rates is essential to avoid melting and deformation. High speeds can result in poor surface finish and excess waste material.
Milling:
Milling plastics can be performed with traditional milling tools or CNC milling machines. Using sharp tools and low cutting speeds helps maintain a good surface finish and minimize melting.
Drilling:
Drilling plastics requires sharp drill bits and appropriate speeds to avoid chipping or cracking. Using coolants can also help prevent overheating.
Laser Cutting:
Hard plastics can be cut using CO2 laser cutting machines or waterjet cutting machines. CO2 lasers produce a clean, sealed edge by cutting with light, while waterjets cut with a high-pressure water stream, resulting in a rougher edge that is not always perpendicular.
Grinding:
Grinding is often used for finishing plastic parts and improving dimensional accuracy. Matching the abrasive material and speed to the plastic type is critical for optimal results.
Sawing:
Sawing is suitable for all types of plastics. Profplastic offers a variety of sawing methods to match specific requirements.
Profiling:
Profiling machines can create desired bevels, grooves, or tapers in plastic components.
Tools and Equipment
Cutting Tools:
Special cutting tools are often used for machining plastics to prevent melting or deformation. Tools with sharp edges and specialized coatings can extend tool life and improve surface finishes.
CNC Machines:
Computer Numerical Control (CNC) machines are commonly used for precise plastic machining. They enable the creation of complex shapes and tight tolerances with minimal human error.
Coolants and Lubricants:
Coolants and lubricants help manage temperatures during machining and extend tool life. This is particularly important when working with thermoplastics sensitive to heat.
Recommendations for Machining Plastics
Cutting Speeds and Feeds:
Start with lower cutting speeds and feeds, and gradually increase to find the optimal balance between speed and finish quality. This prevents overheating and ensures better control of the cutting process.
Tool Wear:
Regularly inspect and replace worn tools to maintain a high-quality surface finish.
Surface Finishing:
Plastics often require post-machining finishing, such as polishing or sanding, to achieve a smooth and aesthetically pleasing result.
Commonly Machined Plastics
- Acrylic (PMMA): Known for its transparency and aesthetic qualities.
- Polycarbonate (PC): Valued for its impact resistance and clarity.
- Nylon (PA): Popular for its wear resistance and strength.
- Polyethylene (PE) and Polypropylene (PP): Frequently used in industrial applications for their chemical resistance.
- Polyoxymethylene (POM) (Delrin): Ideal for precision parts like gears and bearings, as well as applications in the medical, machinery, and food industries due to its high wear resistance.
Machining plastics requires careful optimization of processes and parameters to achieve the best results. By considering the specific properties of the plastic material and employing appropriate tools and techniques, high-quality, precise plastic components can be produced.
Curious about how Profplastic can support your plastic machining needs? Contact us today!