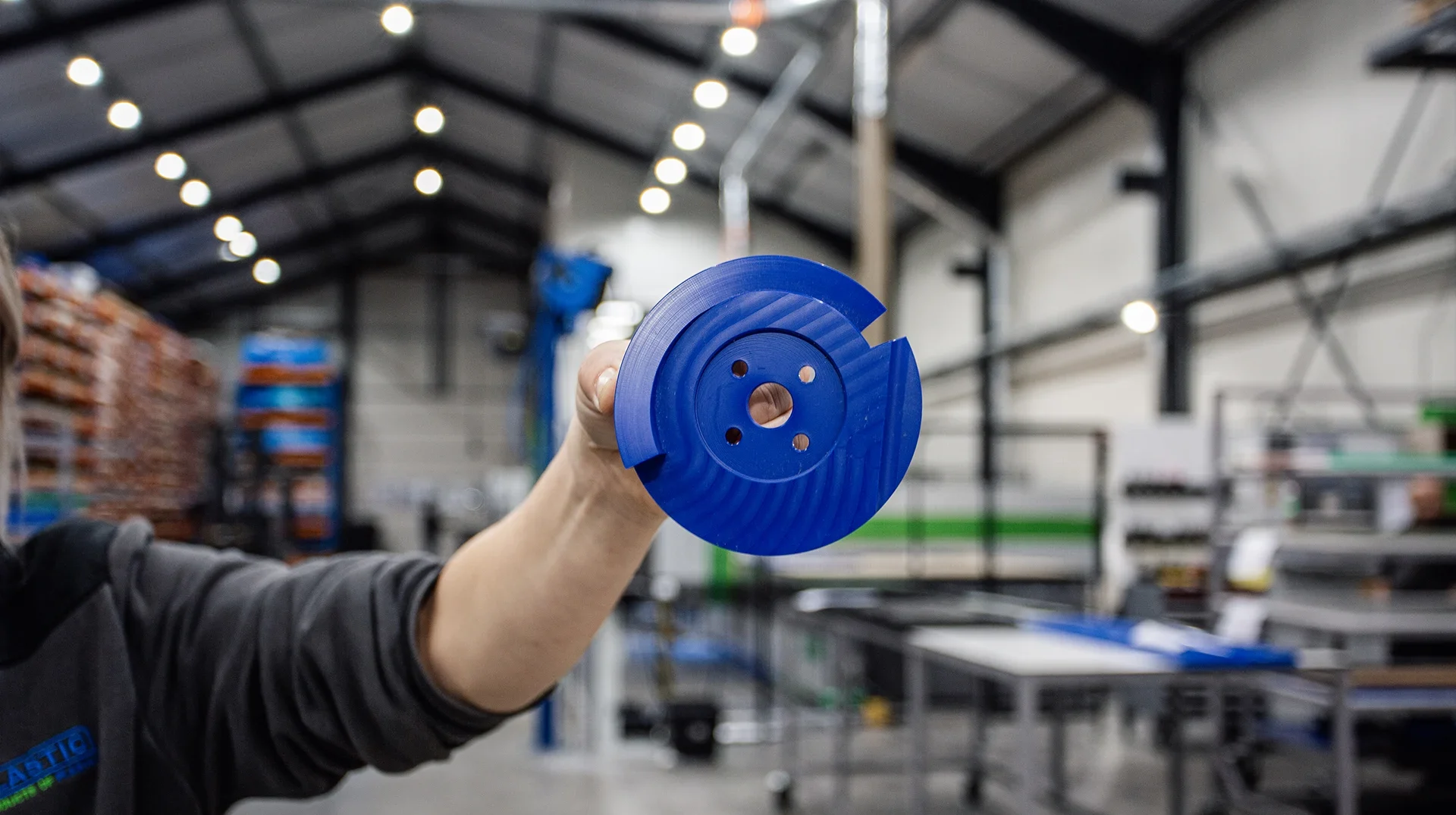
Metal-detectable plastics
Metal-detectable plastics are specially engineered materials that have been treated or modified to be detectable by metal detection equipment. This is particularly important in industries such as food processing, pharmaceuticals, and other sectors where contamination by plastic particles could have serious implications for product safety and quality control. Below is an overview of what metal-detectable plastics are, how they work, and their applications.
What Are Metal Detectable Plastics?
Metal detectable plastics are materials enriched with specific additives, such as metals or metal compounds, that make the material detectable by metal detection systems. These additives are carefully chosen to ensure they do not compromise the normal properties of the plastic while enabling detection through metal detection equipment.
Properties of Metal Detectable Plastics
Detectability:
They are designed to be easily identified by metal detection equipment, which is essential for ensuring product safety and preventing contamination.
Mechanical Properties:
These plastics typically retain the mechanical strength, stiffness, and other functional attributes of the original plastic, though this can vary depending on the type and amount of additives used.
Chemical Resistance:
Metal detectable plastics are often engineered to have similar chemical resistance to their non-detectable counterparts, which is crucial for use in aggressive environments.
Processability:
They can be processed using standard plastic manufacturing techniques such as injection molding, extrusion, and thermoforming.
Advantages of Metal Detectable Plastics
Safety:
They help prevent product contamination by plastic fragments, ensuring consumer safety and compliance with regulations in the food processing and pharmaceutical industries.
Quality Control:
They enable better quality assurance by facilitating the detection of plastic particles that would otherwise be hard to identify.
Cost Savings:
By preventing contamination and reducing the likelihood of product recalls or quality issues, companies can achieve significant cost savings.
Applications of Metal Detectable Plastics
Food Processing:
In the food industry, metal detectable plastics are used for components such as equipment parts, tools, and packaging materials. This prevents contamination of food products with plastic fragments.
Pharmaceutical Industry:
They are used in production equipment and packaging components to prevent plastic contamination in medicines.
Chemical Industry:
Ideal for creating equipment and components resistant to aggressive chemicals while maintaining detectability.
Consumer Products:
In certain cases, metal detectable plastics are incorporated into consumer products where safety is of paramount importance.
Types of Metal Detectable Plastics
- Metal Detectable Polyethylene (PE): Used in applications like packaging and machinery for the food industry, including guides and side rails.
- Metal Detectable Polypropylene (PP): Commonly used in food processing and pharmaceutical equipment.
- Metal Detectable Polyamide (PA): Suitable for mechanical components like gears and bearings.
- Metal Detectable Polyoxymethylene (POM): Ideal for machinery in the food industry, including guides, side rails, and grippers.
Processing and Fabrication
Additives:
Metal detectable plastics are infused with metal particles or other detectable materials during production.
Processing Methods:
These plastics can be processed using standard techniques like injection molding, extrusion, and thermoforming. However, it’s important to ensure the processing does not affect their detectability.
Conclusion
Metal detectable plastics play a critical role in industries where preventing contamination is essential for product safety and quality control. By incorporating detectable materials, these plastics can be efficiently identified by metal detection systems, ensuring the safety and integrity of final products. The choice of the right type of metal detectable plastic depends on the specific application requirements, such as mechanical strength, chemical resistance, and processability.
Curious about the plastics Profplastic supplies to the industry? Contact us today!